top of page
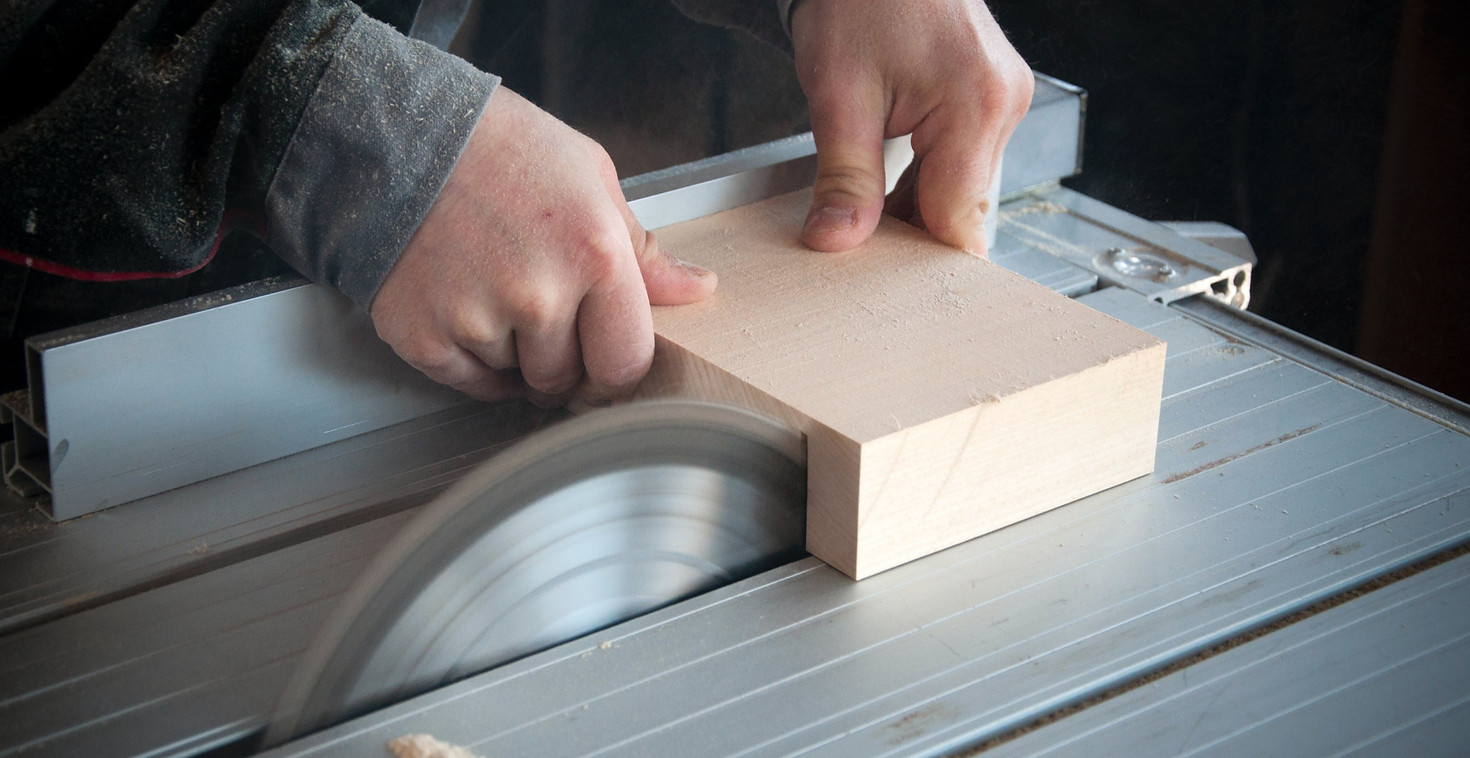
Our Vision and Mission
Next Modular Kitchens has been formed after identifying clear gaps in the market with regards to Product Price, Product finishing quality, Sales & Design Experience, and the installation and after sales.
As a modular kitchen is a once in a life time purchase for most of the consumers, most businesses in the industry do not focus on making sure of an excellent consumer purchase and post purchase experience. We aim to set an extremely high benchmark for our customer’s experience.
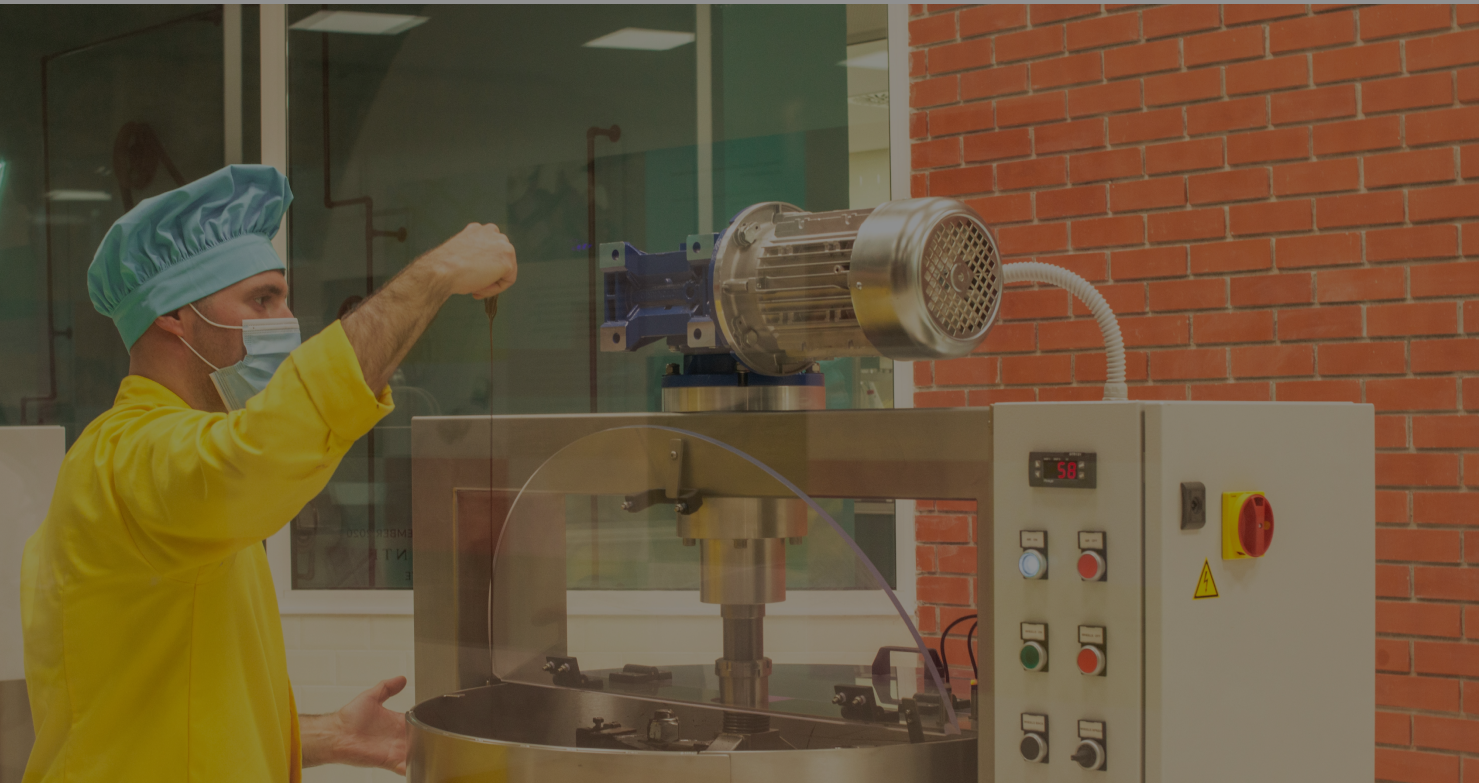
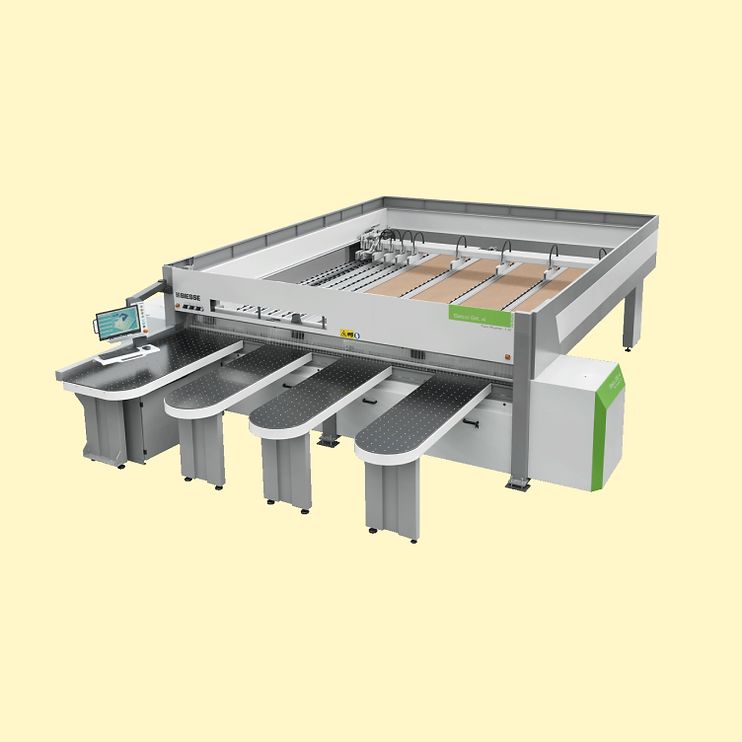
Step 2
Edge Banding
Once the boards have been precisely cut, they undergo the edge banding process to create a polished, finished look. Our advanced automatic edge banding machine applies a seamless edge band to the raw edges, creating a uniform appearance.
The precision of this process ensures invisible edge joint lines, resulting in an extremely high-quality finish that is both visually appealing and durable. Our commitment to using the latest technology and techniques at every step of the production process results in a product that exceeds industry standards and exceeds our customer's expectations.

Step 4
Painting
Achieving a smooth, glossy surface finish is essential for our products, and we take great care to ensure that the boards are free from any foreign particles, such as dust during the painting process. Our use of industrial-grade paint booth's and baking booths ensure that the surface finish of our products is of the highest quality.
Our expert finishing techniques and attention to detail allow's us to produce mirror-like finishes that truly set our products apart. Whether it's for a kitchen or wardrobe, we take great pride in delivering a product that is not only functional but also visually stunning
Step 1
Beam Saw
The first step in our cabinet-making process is the precision cutting of the boards to the required size. Using a state-of-the-art Beam Saw bed, our computer-controlled machinery accurately recognizes and cuts the boards using specialized software.
This automated approach eliminates the possibility of human error and ensures a precise, even cut every time. The smaller pieces produced by the machine are then tagged with a barcode for efficient tracking and assembly. By removing the human touch from this critical step, we guarantee a smooth, uniform edge with no undulations for a perfectly finished product.

Step 3
CNC Drilling & Boring
After edge banding, the boards are then sent to our highly precise drilling machine. This machine automatically reads the program associated with each board's barcode and drills precise holes for the installation of hinges, drawer channels, and other hardware components.
This fully automated process eliminates the possibility of human error and results in a flawlessly drilled product every time. By using state-of-the-art technology and a hands-free approach, we are able to ensure that every aspect of the manufacturing process is executed with the highest level of accuracy and precision.

Join our movement
We would love you to join us in this journey of making democratic designs.
bottom of page